Well its our turn to host the family Christmas dinner at our home. And the first order of business is where do we serve dinner for 22 people. Yep, 22 people. Looking around the house, the obvious place is the garage; it’s large and provides shelter in case of inclement weather. And of course, that means we (my wife, Julie, and I) need to clean the garage. We did this task several years ago and I was proud that we used the Lean principles of 5S:
- Sort
- Set
- Shine
- Standardize
- Sustain
OK, now for my confession. I am good at sorting out what to keep and what not. I am also not bad at setting a place for everything, at least initially. But, I am down right ugly at sustaining the shine on the garage by not putting everything back in its place after its use. Given this its only a matter of time before the garage loses its shine and results in disarray.
Background on Lean and 5S Relationship
Hiroyuki Hirano created 5S. Its purpose is to make a work area efficient and effective prior to a Lean process improvement effort. Five S describes how to organize a work area by identifying/storing items and maintaining/sustaining the order. Historically, analysts have used 5S in manufacturing, but recently 5S has been applied to clerical areas. Unfortunately, 5S has been overshadowed by the Lean process improvement, but no less important.
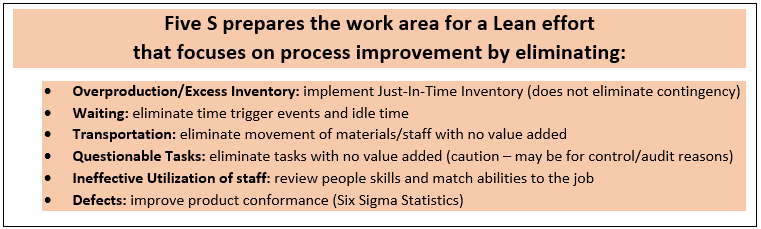
In fact, 5S prepares the work area for Lean process improvement. With that said, let’s review the 5S steps.
Step One – Sort
Separate needed items from the unneeded and dispose of the latter. The Sort goals are to eliminate clutter to achieve an increase in effective use of space and in efficiency in searching for an item.
The first step is to move the cars out to the drive way (assuming cars still fit in the garage) and observe and evaluate the work area. In my case, the garage was not in total disarray from my previous 5 S effort. But, there was evidence of me not sustaining. For example, tools not shining in its designated place. And new items acquired since the last 5 S effort were just randomly placed in the garage with no rhyme or reason. The garage was starting to look like my “junk drawer” in the kitchen and Julie’s art workbench.
Well its time to get the Red Tags. From my previous 5S experience, I know to use red tags to identify items that are possibly not needed or were once needed, but perhaps no longer.

Note, essentially all items are commodities with expiration. I placed each red tagged item in the center of the garage and evaluated them for usefulness, frequency of use, and possibly quantity if necessary. If the item has outlived its need, I need to dispose of it.
Step 2 – Set
Determine a place to store all remaining items. The Set goal is to organize items to further achieve searching efficiency. The next step is to determine a place for all necessary items. For frequently used items, I ensure places are easy to find. In terms of Lean, the place needs to minimize wasted motion (Lean principle) in finding and using the item in a safe way. I would like to emphasize the safety aspect even though it is not originally included in 5S. Diagramming the locations for items is a good approach. Instead of placing a single item, plan the locations on paper.
Step 3 – Shine
Clean the area and place all items in their designated place. The Shine goals are to ensure that items exist in known places.
Categorize (e.g., gardening, automotive, general tools and supplies) the areas and label (text and color) items per your diagram. Besides tidying-up the area, the word clean here encompasses two popular techniques for cleaning up errors. Two popular clean techniques are eliminating user errors (Poka-Yoke, Japanese team) and root cause analysis (Ishikawa/Fishbone diagram along with the 5 whys [2]). Poka-Yoke is simply avoiding an error/injury when using a tool (instructions) like using a face shield with power equipment. Root cause analysis is determining various aspects of why a problem occurs and taking permanent corrective action.
Step 4 – Standardize
Standardize the Sort, Set, and Shine on a consistent basis. The Standardize goals are to ensure that the first three steps are followed to other areas. In my case, I only have one work area – the garage. But, I do occasionally add items. For any new item I need to store in the garage, I need to repeat the three first 5S steps prior to storing it.
With a standard established, I can now apply data analytics (if I choose) to measure process improvements. As data collection progresses, inefficiencies become more apparent so corrective action can be the subject in a follow-on Lean process improvement effort. Note this data collection is a bit of overkill for my garage due to singularity of my case. But, certainly it would be appropriate in a repetitive business environment.
Step 5 – Sustain
Schedule a review of the work area and correct any anomalies. The Sustain goals is to ensure the result of the 5 S method is dependable. Probably the most important step is to promote and maintain the results of the previous four steps. My downfall. I say this although I noted that my next door neighbor has recently cleaned out his garage. Dare I say that I promoted 5S through example? Perhaps my family members might be motivated to clean their garages when they observe the walls of our garage dining area? Regardless, I still need to be better at sustaining the “new world order” in my garage and schedule a regular appraisal (see Summary on Julie’s sign posting). To help me sustain, I am adopting checklists [3] that will help my garage continue the Shine.

Table 1. Summary of Lean 5S

Summary
Five S can be applied in any work environment and prepares a work area for a follow-on Lean process improvement effort. In this case, 5S prepares my garage for Lean process improvement in doing home activities like automobile maintenance, appliance repair, and hobbies like gardening and woodworking. But, remember the preparation benefit is only realized if 5S is sustained. As I said I am the worst (ugly) in keeping the “new world order” in my garage.
Julie to the rescue. She remembered something I wrote about on visual communications. If you want workers to follow management’s policies/business rules, you can’t just verbally say it. People often do not pay attention to what management says. But, they do pay attention to what management measures. For example in some industries, management displays days since the last safety incident or a service outage to remind workers of what is important. So, Julie decided to post a prominent sign in the garage (see below). Note that she highlighted discipline metrics for sustaining Shine and a target for the next 5S review.

P.S. Messy Desks are signs of creativity not efficiency
On the surface, it appears that messy office desks rub against using the 5S Method. In 2012, The Daily Mail [4] reported a German study that a “messy desk” is an indication of a creative mind. Prior to this report, a study of hundreds of CEO's showed executives with high innovation scores also scored low in organizational skills. However, it is important to note that the Lean 5S method was originally designed for manufacturing work areas, not personnel. Five S addresses the efficiency of work areas not the creativity of individuals.
Author: Mr. Monteleone holds a B.S. in physics and an M.S. in computing science from Texas A&M University. He is certified as a Project Management Professional (PMP®) by the Project Management Institute (PMI®), a Certified Business Analysis Professional (CBAP®) by the International Institute of Business Analysis (IIBA®), a Certified ScrumMaster (CSM) and Certified Scrum Product Owner (CSPO) by the Scrum Alliance. He holds an Advanced Master's Certificate in Project Management and a Business Analyst Certification (CBA®) from George Washington University School of Business. Mark is also a member of the Association for the Advancement of Cost Engineering (AACE) and the International Association of Facilitators (IAF).
Mark is the President of Monteleone Consulting, LLC and author of the book, The 20 Minute Business Analyst: a collection of short articles, humorous stories, and quick reference cards for the busy analyst. He can be contacted via - www.baquickref.com.
References/footnotes:
- https://www.psychiatry.org/patients-families/hoarding-disorder/what-is-hoarding-disorder
- https://www.modernanalyst.com/Resources/Articles/tabid/115/ID/1562/Structuring-AS-IS-and-TO-BE-Process-Improvement-Discussions-using-the-Fishbone-Diagram.aspx
- https://www.graphicproducts.com/guides/5s-system/ppc/?_bt=234501290601&_bk=%2Bfive%20%2Bs&_bm=b&_bn=g&_bg=40201443557&gclid=EAIaIQobChMIoueG_tb45QIVTZyzCh3x4QF_EAAYASAAEgL2E_D_BwE
- http://www.dailymail.co.uk/sciencetech/article-2088359/Messy-desks-office-actually-lead-employees-think-clearly-say-researchers.html