Reading time for this article is 8-10 minutes. The purpose of this article is to cite an example of using Lean-Agile project management for a small home construction project – a bathroom remodel. The remodeling firm unknowingly uses a Lean-Agile project approach that was the result of lessons learned over years of experience. In fact, when I questioned the remodeling firm about Lean-Agile, the firm’s response was “What is that?” Regardless of what you call it, the firm uses their construction approach because it works.
Note this article cites concepts such as user stories, job stories, user story mapping, gemba walk, communication channels, grooming, agile scaling as well as elements of Lean-Agile project management.
The Project
My wife and I had a conversation on improving the quality of our home life. Soon into our dialogue, our focus centered on a master bath remodel. We both agreed that this would improve our visits to the bathroom, in particular during the wee hours of the night. So we started writing user stories and even prioritized them 1. Yes, our own product backlog. Below is an excerpt of those stories that we felt would improve the look and feel of our master bath.
User Stories (our initial Product Backlog)
1. As a peritoneal dialysis patient, I want a heated toilet seat 2 so that my half-asleep warm posterior can avoid having to bear (burr) with an ice cold toilet seat in the wee hours of the dead of winter.
Job Story version 3 - When I am in bed and need to use the bathroom in the wee hours of the dead of winter, I want to avoid having to bear with an ice cold toilet seat so that my half-asleep warm posterior allows me to return to sleep.
2. As a peritoneal patient, I want a heated tile floor 2 so that my half-asleep bare feet would avoid having to bear (burr) with a cold tile floor in the wee hours of the dead of winter.
Job Story version 3 - When I am in bed and need to use the bathroom in the wee hours of the dead of winter, I want to avoid having to bear with a cold tile floor so that my warm bare feet allow me to return to sleep.
3. As home owners, we want a larger shower so that we won’t feel claustrophobic when bathing.
4. As home owners, we want a larger linen closet so we have more room for bath towels and bed sheets as well as bath supplies.
5. As home owners, we want a larger medicine cabinet so that we have more room to store our medications (with age comes more pills; due to our frequent visits to our drugstore, the pharmacist now calls us by our first names).
6. As home owners, we want to replace the vanities to be taller, lighting and plumbing fixtures to have a modern look; it looks so “2000.”
7. As home owners, we want to have two stained glass windows with a continuous nature scene to add some beauty to the bathroom.
8. As home owners, we want to remodel our master bath 4
- within the footprint of the current bathroom,
- utilizing our current A/C and electric hot water systems,
- be secure under our current security system.
User Story Map
Realizing that our user stories were epics, we broke down our large stories into smaller stories and finally features (each on separate index cards) and arranged them underneath the associated epics creating a user story map 5. For example, the shower area featured
- two small benches
- an overhead rain shower plus a hand held sprayer
- two transom windows with stained glass inserts
The map structure allowed us to tell our remodel story (vision) to ourselves and others who would listen (family and friends) especially a builder. This structure is better than just listing the stories randomly.
Finding a Builder
Recognizing our lack of construction expertise, we both agreed that we needed to hire a professional firm to do the remodel. This means facing the scariest word in the English language – estimate. So we asked for a number of bid proposals from firms with good reputations. To my surprise the firm we liked best appeared to use a Lean-Agile project approach. We had heard of firms outside the world of software development using agile, but never experienced it first hand and as home owners.
Expectations – Traditional Project Management
Since we had contracted the building of our home several years ago, we had expectations from the remodeler.
- Formal specifications with blueprints and a formal change process
- Delays during the project due to waiting on supplies
- A down payment of 20-50% of the fixed price up front and the rest at completion after reviewing a punch-list of remaining work
- Infrequent communications after the signing of the contract (i.e., the project manager will advise the home owners of any problems via a formal channel)
- A project manager that directs workers on how the work is to be accomplished
Segment Releases – The Lean-Agile Approach
Without a detail requirements document, we signed a high-level document with a total constraint 6 of $60K and gave the typical 20% down payment. The document included a schedule of incremental segments of work with associated payments, similar to minimum viable products in agile software development.
- Rough framing, plumbing, and electrical
- Cabinetry built and start of tile work
- Completion of tile work and start of countertops
- Completion of punch list
Work would not start until all building supplies were available and stored in our garage. This utilized just-in-time inventory and eliminated transportation delays 7 once the project started. Upon the completion of each segment, the firm asked us to inspect the progress and per our satisfaction pay the associated incremental payment.
Daily Meetings and Direct Communications
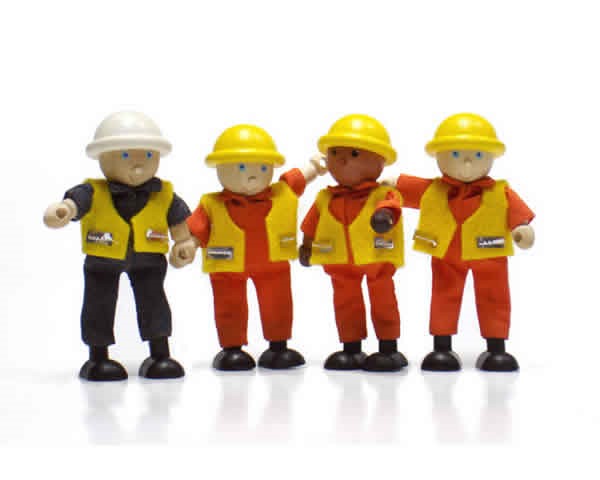
|
|
Each day of the remodel, the Project Manager and Customer Advocate (quality manager) met with the small team of workers and ourselves at the work site (Gemba Walk) 8. We reviewed what was done the day before and what the team had scheduled for that day. The PM then asked if there were any road blocks (impediments) in accomplishing the work that the manager could assist the team in removing 9. The PM and customer advocate asked us if we had any questions and encouraged us to communicate with the team and directly with the workers; in fact our communication was continuous rather than infrequent 10. The PM wrapped-up the meeting asking the team for any noted improvements (retrospective) in process, equipment, and/or supplies.
Quick Resolution at Minimum Cost
Were there problems? Sure there were; just like all projects – like a wrong tile delivery and inconsistent messages. We also had emergent requirements to some bathroom features and some work corrections, but by embracing change we were able to resolve things quickly and avoid rework (i.e., not wait until the finish of the remodel. For instance with little hassle, we:
- changed the length of the shower walls,
- added an electrical plug-in for the heated toilet seat,
- corrected an under-the-counter sink mount,
- resized the stained glass windows,
- reinforced a ceiling for a heavy light fixture,
- and installed slide-out shelves in the cabinetry.
And as in Lean-Agile, we delayed decisions on the:
- size and framing of mirrors,
- selection of plumbing and lighting fixtures,
- vanity furniture and cabinet hardware,
- design of stained glass,
- size of closet doors and sliding shelves,
- color of wall paint and wood stain,
until the last possible moment that information was available. But even with these Lean-Agile practices, we still needed to blend our lessons learned from traditional project management like being specific on our requirements, using measurements, ensuring our needs were achievable and relevant within our timeframes (i.e., SMART objectives).
Project and Business Success
Well even with its ups and downs, the project was a success with caveats: scope complete plus changes, 30% schedule overrun (45 days rather than 30 days), but within 5% of the budget due to our additions 11. But most important, we are enjoying the qualitative benefits. Yes, it was a business success in terms of personal comfort. Warm and toasty, we are enjoying a beautiful, modern looking bathroom even in cold weather.
Lessons Learned
I am more convinced that the Lean-Agile approach can be successfully used outside the world of software development. At least for small construction projects like our bathroom remodel, Lean-Agile works quite well. Although, I must admit that the infamous 95% completion status that seems to take forever to complete exists in construction as in software projects; my feeling is that this phenomenon is due to starting a new project prior to finishing the current project (i.e., multitasking).
By-the-way, the remodeling firm has been using the Lean-Agile approach for several years. They based their process over 30 years of continuous improvement and lessons learned (i.e., best practices).
Large Scale Projects
How well Lean-Agile scales to large construction projects needs to be experienced and cited. We certainly know there are large scale approaches for large software development projects such as LeSS, Scrum-of-Scrums, and SAFe®. However, large construction projects have unique challenges with large budgets and typically involve many subcontractors. Perhaps, a hybrid approach (a mixture of waterfall and agile) is appropriate. But, the formal requirements document of traditional project management maybe just as vital due to the nature of the project.
P.S.
As I sit here admiring our new oasis, I contemplate the value of a plan in traditional project management. We assume the plan is everything. But that is just not reality. Eisenhower reminds us, “Plans are nothing, planning is everything.” He certainly realized this on planning D-Day, (i.e., once you hit the beach, you have to adjust to the situation).
The real measure of value, in this context, is the agility of the plan (i.e., managing changes).
|
With Lean-Agile, we do just enough initial planning to pave a dirt road in the direction of our goal with the understanding that there will be twists and turns in our journey to the finished highway. In other words, embrace and brace for the changes ahead.
Author: Mr. Monteleone holds a B.S. in physics and an M.S. in computing science from Texas A&M University. He is certified as a Project Management Professional (PMP®) by the Project Management Institute (PMI®), a Certified Business Analysis Professional (CBAP®) by the International Institute of Business Analysis (IIBA®), a Certified ScrumMaster (CSM) and Certified Scrum Product Owner (CSPO) by the Scrum Alliance. He holds an Advanced Master's Certificate in Project Management and a Business Analyst Certification (CBA®) from George Washington University School of Business. Mark is also a member of the Association for the Advancement of Cost Engineering (AACE) and the International Association of Facilitators (IAF).
Mark is the President of Monteleone Consulting, LLC and author of the book, The 20 Minute Business Analyst: a collection of short articles, humorous stories, and quick reference cards for the busy analyst. He can be contacted via - www.baquickref.com.
References/footnotes:
- Note that the format I chose to use here is user stories since this is a construction project. However, I could have used job stories instead (see reference note 3). In software development projects, I prefer the details of use case conversations when documenting needed capabilities for a system.
- The top two requirements are due to my wife’s medical condition; she is a peritoneal dialysis patient and constantly feels cold. For these two user stories, I also provided Job Stories 3 for comparison. A job story may be used when more than one user shares a common goal – no need to be role specific (I definitely will share/enjoy the heated benefits
as will my wife). Also, note that the style of the job story is focused on user motivation rather than the problem solution as in the user story.
- The job story is a concept developed by Alan Klement. See the book “The Innovator’s Solution” by Clayton Christensen and Michael Raynor published by Harvard Business School Press.
- User story number 8 lists nonfunctional requirements or constraints. Other constraints could be budget and time frame. Previous stories (1-7) are functional requirements.
- The user story map is a concept developed by Jeff Patton. See his book “User Story Mapping” published by O’Reilly.
- Only the installation of the bathroom fixtures were included in the budget, not the cost of the fixtures.
- However, limiting motion was a challenge since the bathroom space was not large enough to accommodate some equipment like tile and lumber saws. Workers needed to make many trips to the garage to use this equipment; fortunately the supplies were in the garage.
- Gemba Walk is Japanese for “the real place.” It denotes visiting the actual work site, seeing the process, understanding the work, asking questions, and learning.
- Note the PM and Customer Advocate also had a quality management role like a chef in a restaurant inspecting dishes prior to waiters serving the customers. They reviewed the work as it was being accomplished and ensured it met their standards – showcase quality. For example, the PM advised a worker that the shower floor membrane was too short and had to be higher on the inside walls to ensure there would be no water leaks. Also, the Customer Advocate had some marred wood paneling replaced for an improved visual effect. In both cases, rework (technical debt) was incurred, but at a much lower cost than waiting until the shower was tiled and the wood paneling stained.
- This is a true characteristic of Lean-Agile. Having direct communications is good. But, the number of communication channels to manage is a challenge (i.e., the # of channels = ((# of people) X (# number of people – 1)) / 2. For example: there are 15 channels to manage with 6 people: 6 x (6 - 1) / 2.
- Caveats: We installed a 220 electrical line for the heated floor, moved a water line for the heated toilet, reinforced the ceiling for a heavy lighting fixture, added crown molding, ordered beveled mirrors with custom frames plus some other amenities (i.e., the grooming of the product backlog). Also, we outsourced the stained glass work and heated toilet installation to separate firms due to expertise and warranty considerations. Some stained glass work was done post project.
|
We both agreed that this would improve our visits to the bathroom, in particular during the wee hours of the night.
|